Plastic extrusion for creating standardized, top-grade parts
Plastic extrusion for creating standardized, top-grade parts
Blog Article
A Comprehensive Guide to the Refine and Benefits of Plastic Extrusion
In the substantial realm of production, plastic extrusion emerges as a necessary and extremely efficient process. Altering raw plastic right into constant profiles, it caters to a plethora of sectors with its remarkable adaptability.
Comprehending the Basics of Plastic Extrusion
While it may appear complex at very first look, the process of plastic extrusion is essentially easy - plastic extrusion. It is a high-volume manufacturing method in which raw plastic is melted and shaped into a constant profile. The process begins with the feeding of plastic material, in the kind of pellets, granules, or powders, right into a heated barrel. The plastic is after that melted making use of a combination of heat and shear, applied by a revolving screw. As soon as the molten plastic gets to completion of the barrel, it is forced through a tiny opening referred to as a die, forming it into a desired kind. The designed plastic is after that cooled, solidified, and cut right into desired sizes, completing the procedure.
The Technical Refine of Plastic Extrusion Explained
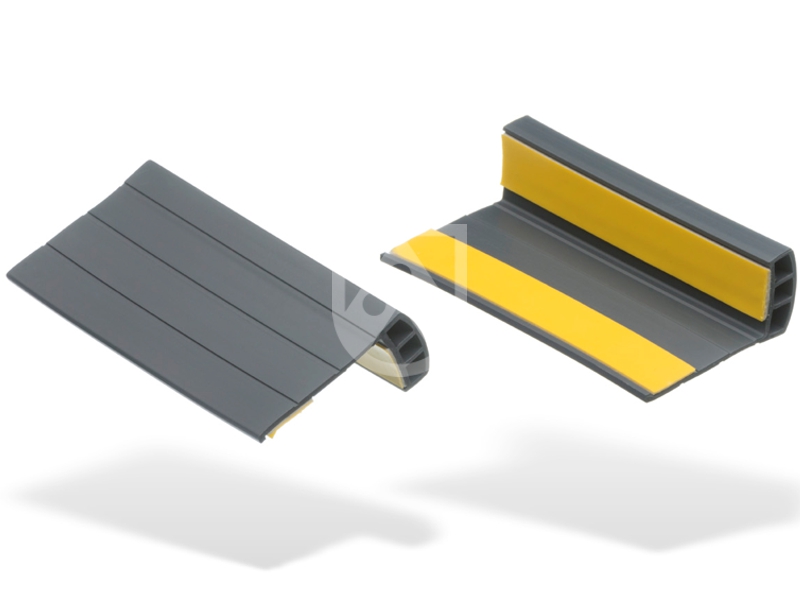
Kinds Of Plastic Suitable for Extrusion
The choice of the best kind of plastic is an essential facet of the extrusion procedure. Various plastics use unique properties, making them more matched to specific applications. Comprehending these plastic types can considerably improve the extrusion process.
Contrasting Plastic Extrusion to Various Other Plastic Forming Approaches
Comprehending the kinds of plastic ideal for extrusion leads the way for a wider conversation on exactly how plastic extrusion stacks up against various other plastic forming techniques. Plastic extrusion is unrivaled when it comes to creating constant profiles, such as gaskets, pipelines, and seals. It also allows for a consistent cross-section along the size of the product.
Trick Benefits of Plastic Extrusion in Production
In the world of manufacturing, plastic extrusion provides numerous considerable advantages. One significant advantage is the cost-effectiveness of the process, that makes it a financially enticing production approach. In addition, this technique offers superior product flexibility and enhanced manufacturing speed, consequently boosting general production efficiency.
Affordable Manufacturing Technique
Plastic extrusion jumps to the forefront as an economical production approach in production. This procedure sticks out for its capacity to generate high quantities of material quickly and successfully, supplying manufacturers with substantial financial savings. The primary expense advantage is the capability to make use of more economical basic materials. Extrusion utilizes thermoplastic materials, which are less costly contrasted to metals or ceramics. Better, the extrusion process itself is relatively easy, reducing labor costs. Furthermore, plastic extrusion needs less power than traditional manufacturing methods, adding to reduced operational costs. The procedure also reduces waste, as any kind of excess or faulty materials can be reused and reused, offering an additional layer of cost-effectiveness. In general, the monetary benefits make plastic extrusion a very appealing option in the production industry.

Superior Product Adaptability
Past the cost-effectiveness of plastic extrusion, one more significant advantage in making lies in its exceptional item flexibility. This makes plastic extrusion a suitable remedy for markets that need personalized plastic components, such as automobile, building, and product packaging. In significance, plastic extrusion's product adaptability cultivates development while boosting functional efficiency.
Boosted Manufacturing Speed
A substantial important site advantage of plastic extrusion depends click now on its enhanced manufacturing rate. This manufacturing process enables high-volume manufacturing in a reasonably brief time period. It can generating long, constant plastic accounts, which considerably reduces the production time. This high-speed manufacturing is particularly helpful in markets where big amounts of plastic parts are needed within tight deadlines. Couple of various other production processes can match the rate of plastic extrusion. Furthermore, the capacity to maintain consistent high-speed production without sacrificing item high quality sets plastic extrusion besides various other methods. The improved production rate, therefore, not just allows makers to fulfill high-demand orders but additionally adds to raised effectiveness and cost-effectiveness. This helpful feature of plastic extrusion has actually made it a preferred choice in numerous markets.
Real-world Applications and Effects of Plastic Extrusion
In the world of manufacturing, the strategy of plastic extrusion holds profound relevance. This procedure is widely utilized in the production of a variety of products, such as plastic tubes, window structures, and weather removing. Because of this, it greatly influences fields like building, product packaging, and auto sectors. Its effect extends to everyday items, from plastic bags to tooth brushes and disposable flatware. The financial benefit of plastic extrusion, largely its high-volume and cost-efficient result, has reinvented manufacturing. The environmental influence of plastic waste stays an issue. Consequently, the sector is persistently pursuing technologies in biodegradable and recyclable materials, showing a future where the advantages of plastic extrusion can be retained without endangering environmental sustainability.
Verdict
Finally, plastic extrusion is a highly reliable and effective method of transforming basic materials right into diverse items. It supplies countless advantages over various other plastic forming techniques, consisting of cost-effectiveness, high output, marginal waste, and design flexibility. Its effect is exceptionally felt in numerous markets such as building and construction, automobile, and consumer goods, making it a pivotal procedure in today's manufacturing landscape.
Diving much deeper into the technical process of plastic extrusion, it begins with the selection of the suitable plastic material. Once cooled down, the plastic is reduced into the required lengths or wound onto reels if the item is a plastic movie or sheet - plastic extrusion. Contrasting Plastic Extrusion to Other Plastic Forming Techniques
Comprehending the kinds of plastic appropriate for extrusion paves the way for a more comprehensive discussion on how plastic extrusion stacks up against various other plastic developing important link methods. Few other manufacturing processes can match the speed of plastic extrusion.
Report this page